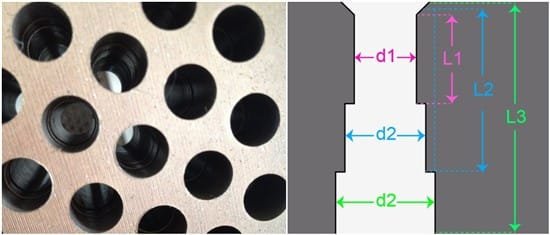
Before the pellet maker mold is made use of, the compression ratio must be changed and calculated. This is mainly to readjust the size of the mold and mildew, the thickness, the taper and reaming level of the bell mouth, the product of the mold, the hardness of the mold and mildew, as well as various products, there are different mold compression ratios.
So we have to readjust and calculate according to our real situation, so what is the adjustment computation approach of the pellet machine mold compression ratio?
Compression Ratio Of Pellet Machine Mold
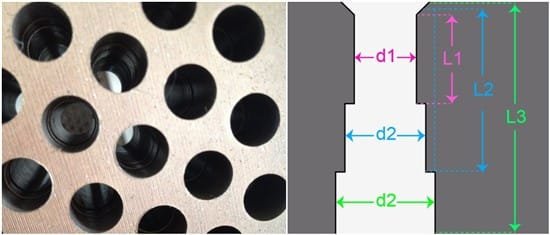
The compression ratio of the pellet machine die describes the ratio of the effective length of the die opening of the die to the die size, and is an index reflecting the extrusion stamina of the pellet equipment.
Pellet maker mold and mildew compression ratio = mold and mildew opening size/ reliable working length of mold and mildew opening
For a mold and mildew with a straight hole, the efficient size of the mold opening is the overall thickness of the mold, and also the tiny diameter is the size of the mold opening itself.
Presumption: The size of the die hole is 6mm, and the density of the ring die is 45mm
Compression ratio= 6/45= 1:7.5.
The ring mode compression ratio is 1:7.5.
For the release action hole as well as the outer conical hole, the reliable size of the die hole is the overall density of the mold minus the length of the launch opening or the length of the external tapered opening, as well as the aperture of the small diameter area is the aperture for calculating the compression ratio.
Assumption: the diameter of the ring die hole is 8mm, the die thickness is 66mm, as well as the launch opening is 18mm.
Compression ratio= 8/( 66-18)= 1:6.
The ring mode compression ratio is 1:6.
Compression ratio is a ratio. For the same compression ratio, its aperture and effective functioning length might be various.
Just how To Choose a Suitable Mold And Mildew Compression Ratio?
1. The aperture dimension and result of the mold are closely pertaining to the inner diameter of the pellet equipment mold as well as the composition of the raw materials. The standard aperture of 8-10 mm generally used in the industry is called standard information.
The pellet machine larger than 10 mm needs greater pressure for molding., Reasonably talking, the wear is additionally big, users generally call it a biomass pole making machine or a rod making machine.
2. The efficient density of the mold is extremely vital for the molding of basic materials.
If the mold is as well thick, the molding time of the raw material is longer, the density of the bits is relatively large, the extrusion is more difficult, the mold and mildew is slim as well as very easy to damage, and also the density of the bits is reasonably little.
Journalism temperature is low, the result is high, but the molding price is low or the molding is poor.
3. The compression ratio of rough devices is identified according to the raw products. The compression ratio of poplar wood is 1:6, the compression ratio of yearn wood is 1:7, the compression ratio of hard wood is 1:5, and the compression ratio of shavings is 1.: 5.5, the compression ratio of corn stalk is 1:6.5.
From these basic figures, the compression ratio of various basic materials is various. The more difficult the raw material, the smaller the compression ratio, and also the cosy the raw product, the greater the compression ratio.
That is to state, the extra cosy the raw product, the much easier it is to be built. The even more cosy resources consists of a lot more fibers, and the even more fiber-containing materials are much easier to shape.
4. Each little opening straight has 6 mm, 8 mm, and also 10 mm. This 1 stands for the size of each small opening. If the diameter of the ring die hole is 8 mm, then this 1 represents 8, And 6 stands for the effective aperture.
The effective aperture is equal to the size of the hole multiplied by the efficient aperture length, which is 6 * 8= 48, which is 8:48, 8:48 is streamlined to 1:6, 1: 6 is the compression ratio of poplar wood. It is converted in this way.
The quality of the biomass pellet maker’s output depends upon the compression ratio of the ring die. However if the client does not have high requirements for the molding rate of your pellets, after that you can appropriately Decrease the compression ratio, which can not just enhance the result, yet also minimize the life span of the mold and also the pressing wheel.
5. Roughness is also a vital indication to measure the quality of ring die. Under the exact same compression ratio, the greater the roughness worth, the greater the extrusion resistance of the sawdust fragments, and the more difficult it is to discharge the material.
Too much roughness likewise impacts the quality of the fragment surface area. The proper roughness worth ought to be 0.8-1.6. in between.
What To Do If The Mold And Mildew Compression Ratio Is Too Huge ?
1. Experienced operators will change the moisture material of the raw products or readjust the void in between the ring molding rollers, and the pellets can be efficiently discharged without changing the compression ratio. The process needs to be taped and also checked step by step.
2. Additionally, the 2nd pressurization can make the mold with a larger compression ratio smaller, yet changing the ring mold and mildew will affect the hardness of the ring mold, so it needs to be determined according to the real wear of the mold and mildew.
The roughness of the die opening of the pellet equipment is additionally a vital indicator to measure the high quality of the mold, as well as the suitable roughness value should be between 0.8-1.6.
Under the exact same compression ratio, the larger the roughness worth, the greater the fragment extrusion resistance, and the harder it is to release the material. Excessive roughness additionally impacts the top quality of the bit surface area.