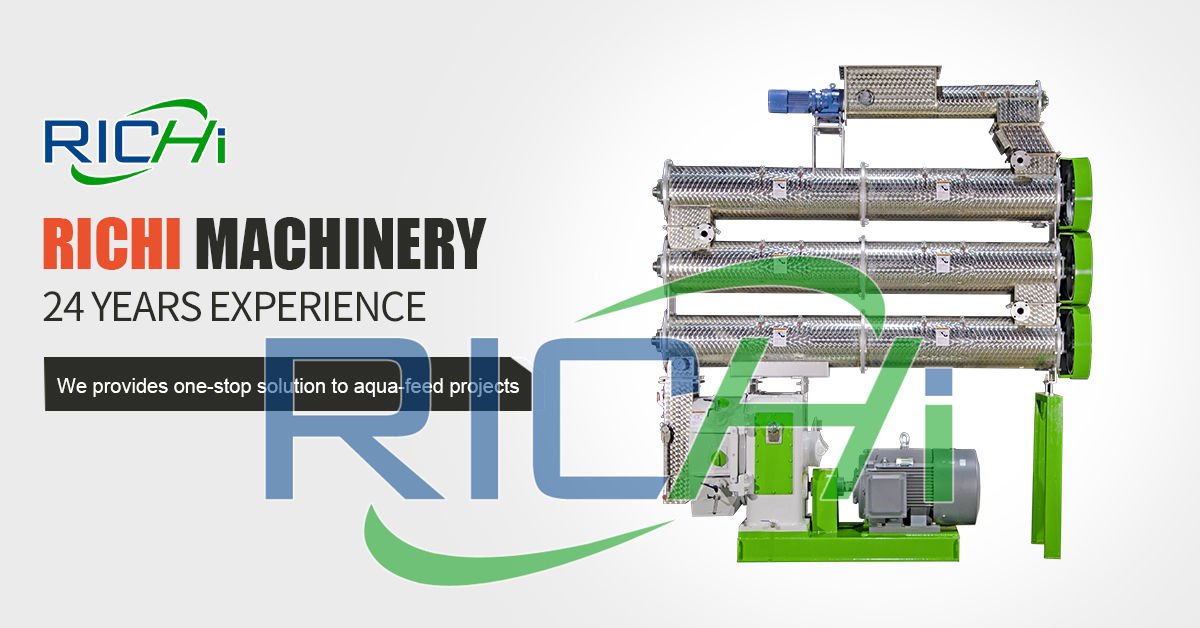
As we all know, the poultry making machine is named for the smooth surface of the feed produced, the high hardness of the pellets, and the internal curing, which can improve the nutrient absorption of animals. According to different raw materials, pellets that can be eaten by livestock are directly produced through the pressing of the poultry making machine.
However, during a recent return visit to an old customer, our staff found some problems caused by improper use of the poultry feed pellet making machine. The following are a few problems and solutions that Richi Machinery has compiled for you.
1.Are the produced pellets bent and cracked?
Reason: This situation is often caused by the pellets leaving the poultry feed pellet making machine. When the position of the cutter is adjusted farther from the surface and the knife edge is dull, the pellets are broken or torn by the cutter instead of being extruded from the die hole.
Cut off, at this time some pellets are bent to one side and many cracks appear on the other side. During the process of entering the cooler for cooling or transportation, the pellets tend to break from these cracks, resulting in too much pellet powder produced. (Related post: cat litter making machine)
Improvement method:
- Increase the compression ratio of the mold, thereby increasing the density and hardness of the pellets.
- Grind the raw materials finer to increase the density of pellets and prevent the feed from being loose.
- Adjust the distance between the cutter and the die surface or replace the cutter with a sharper one.
(2) Is the surface of the pellets uneven?
This situation is that the powder used for granulation contains raw materials with large pellets that have not been crushed or semi-crushed. Due to insufficient softening during the poultry making machine conditioning process, the pellets are relatively hard and relatively large. After passing through the mold of the poultry making machine, when the pores are not well combined with other raw materials, the pellets appear uneven.
Improvement method: properly control the thickness of powdered feed, so that all raw materials can be fully softened during conditioning; for raw materials containing more fiber, steam bubbles are easily mixed, so do not add too much to this formula. lots of steam. (Related post: cat litter production line)
(3) Is the color of individual pellets or pellets inconsistent?
This situation is common in the production of aquafeed, mainly manifested in that the color of individual pellets extruded from the poultry making machine is darker or lighter than that of other normal pellets, or the surface color of a single pellet is inconsistent, thus affecting the appearance quality of the whole batch of feed.
Improvement method: mainly to control the mixing uniformity of each component in the formula and the mixing uniformity of the added water; improve the tempering performance, control the tempering temperature if necessary, and use a lower tempering temperature to reduce the color change ; Control the return material.
For formulas that are prone to “uneven color”, try not to use the return material to directly granulate. The return material should be mixed with the raw materials and then smashed again. The mold with guaranteed quality is used to control the size of the die hole. Finish, sand the die hole if necessary before use.
2.Working principle of RICHI poultry making machine
Ring die poultry making machine is one of the main equipment of RICHI poultry pellet feed production line, the feed from powder state to pellet formation should be completed through four areas:
(1) The material is transported to the modulator through the speed-regulating feeding auger. In order to obtain good granulation benefits (increase output and quality), after adding hot steam for conditioning, the material is brought close to the ring die cover and the inner wall of the die (feeding area) by gravity and centrifugal force generated by the rotation of the ring die.
(2) Under the action of the cutting knife, the wedge-shaped space (compression zone) formed by each pressing roller and the ring die is fed uniformly and continuously.
(3) Since the gap between the working surface of the outer wall of the pressure roller and the working surface of the inner diameter of the ring die is only 0.1-0.3mm, and the gap is basically horizontal, a certain extrusion force (extrusion area) is formed.
(4) Due to the feeding, under the strong extrusion between the die and the roller, the material is compacted, squeezed into the die hole, and formed in the die hole (forming zone).
The material continuously enters the pressing area, is extruded and continuously extruded from the die hole, and is cut into various desired pellet lengths from the distance between the adjustable knife edge and the outer wall of the ring die.
3.What is the reason for the different sizes of feed pellets?
Feed machinery and equipment is a kind of machinery for processing feed. It is widely welcomed by people for its unique advantages. However, in use, different sizes are prone to occur. At this time, we need to solve it reasonably. Before solving, we need to understand the difference. The reason for the size is to bring convenience to our use, so what are the reasons for the different sizes of the feed pellet machine?
(1) Feeder blade. Gear: The formation of feed pellets mainly depends on the rolling of the pellet machine gear and the cutting of the moving blade. Once the gears or blades may cut the feed pellets with uneven thickness and length.
(2) Motor: The motor equipped with the feed pellet machine is a motor suitable for its rated power. Once it is damaged during operation or the operating power is unstable, it cannot be pelletized or pelletized unevenly.
(3) Operation: Due to the irregular operation of the operator, the pellet feed processing machinery will also produce uneven pellets. For example, pellet powder contains a lot of water, so that feed pellets do not form, and cold cracks may be formed. If this happens, operators should calmly analyze, find out the reasons, and make up for it in time, so as not to affect the output value of pellets and cause corresponding economic loss.
When feeding the poultry making machine, we must pay attention to different feeding sizes, because different feeding sizes are not only easy to cause equipment blockage, but also easy to cause equipment damage, thus affecting our normal work, which requires us to use, strengthen maintenance, to extend the efficiency of poultry making machine usage.