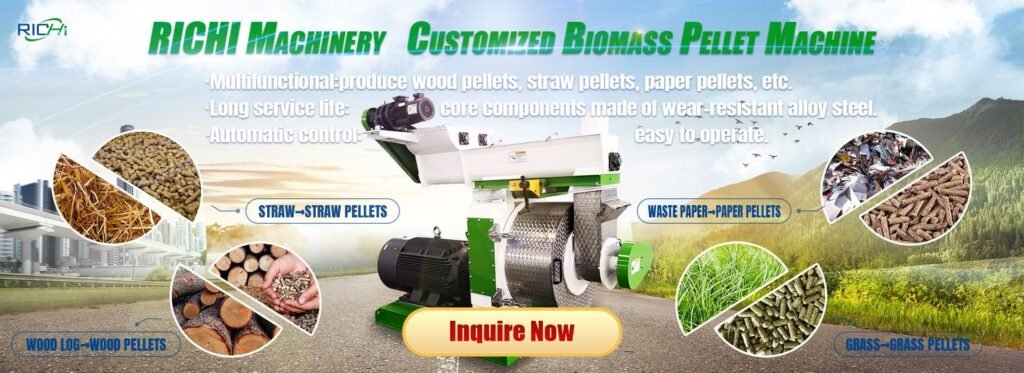
Small biomass pellet machines play a vital role in transforming various biomass materials, such as wood, agricultural residues, and organic waste, into high-density pellets. These pellets are a sustainable energy source and are used for heating, power generation, and animal bedding. The performance of a small biomass pellet machine is significantly affected by its components. Understanding how these components function and interact can help users optimize their machines for enhanced efficiency and output. This article examines the main components of a small biomass pellet machine and their impact on performance.
1. Pellet Die
The pellet die is one of the most crucial components of a biomass pellet machine. It is responsible for compressing and shaping the raw materials into pellets.
- Function: The die consists of a circular plate with holes of specific diameters. As biomass is forced through these holes, it is compressed into cylindrical pellets. The number and size of these holes determine the diameter and shape of the resulting pellets.
- Material: The die is typically made from high-quality steel, such as stainless or alloy steel, ensuring durability and wear resistance. A well-constructed die can significantly improve machine performance by providing consistent pellet quality and reducing the need for frequent replacements.
- Impact on Performance: The design and condition of the die directly influence the efficiency of the pelletizing process. A worn or damaged die can result in poor pellet quality, increased energy consumption, and lower output. Regular inspection and maintenance of the die are essential for optimal performance.
2. Rollers
Rollers work alongside the die to compress biomass material into pellets.
- Function: Rollers apply pressure to the raw material as it passes through the die. Their design and configuration are crucial for ensuring that the material is adequately compressed and shaped.
- Material: Rollers are generally made from high-strength steel and may be treated to enhance hardness and wear resistance. The roller surface can be smooth or textured, depending on the type of material being processed.
- Impact on Performance: The rollers’ effectiveness in compressing biomass affects the overall efficiency of the pelletizing process. If rollers do not maintain proper contact with the die, it can lead to slippage, reduced pressure, and inconsistent pellet quality. Proper alignment and maintenance of the rollers are vital for optimal performance.
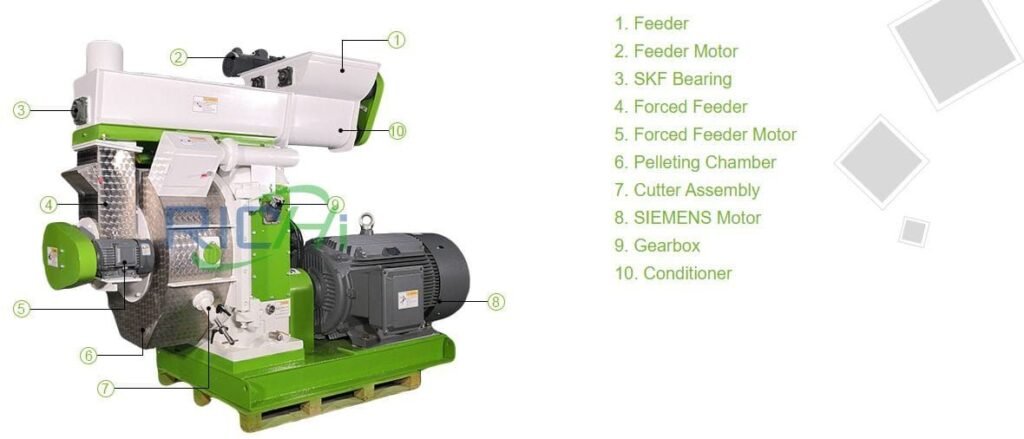
3. Feed Hopper
The feed hopper serves as the entry point for raw materials into the pellet machine.
- Function: The hopper regulates the flow of biomass into the machine, ensuring a steady supply for continuous operation.
- Design: A well-designed feed hopper facilitates easy loading and prevents blockages. Some hoppers are equipped with sensors to monitor material levels and maintain consistent feeding.
- Impact on Performance: An improperly functioning feed hopper can result in uneven feeding, causing fluctuations in pellet quality and production rates. Keeping the hopper clean and free from obstructions is crucial for a consistent flow of raw materials.
4. Conditioner
The conditioner is an optional but valuable component that can enhance a biomass pellet machine’s performance.
- Function: The conditioner adds steam or moisture to the raw materials before they enter the pellet mill. This process softens the biomass and improves its binding properties, making it easier to pelletize.
- Impact on Performance: Proper conditioning can result in higher pellet density, improved durability, and reduced energy consumption during the pelleting process. It also minimizes wear on the die and rollers by reducing friction. Conditioning is particularly beneficial for materials with high lignin content, such as wood.
5. Gearbox
The gearbox is responsible for transmitting power from the motor to the pellet mill.
- Function: It converts the high-speed rotation of the motor into the appropriate speed and torque needed for the pelletizing process.
- Impact on Performance: A high-quality gearbox ensures efficient power transmission, which is essential for maintaining consistent production rates. If the gearbox malfunctions, it can lead to reduced output and increased energy consumption. Regular maintenance and lubrication of the gearbox are essential for optimal performance.
6. Motor
The motor is the driving force behind the pellet machine.
- Function: It powers the entire operation of the pellet mill, including the die, rollers, and additional components.
- Impact on Performance: The motor’s size and efficiency directly affect the machine’s output capacity. A motor that is too small may struggle to maintain the required pressure for pelletizing, leading to decreased performance. Conversely, an oversized motor can lead to unnecessary energy consumption. Selecting the appropriate motor size based on the machine’s production capacity and material type is crucial.
7. Cooling System
Once the pellets are formed, they need to be cooled to maintain quality and prevent spoilage.
- Function: The cooling system reduces the temperature of the hot pellets, allowing them to harden and stabilize.
- Impact on Performance: Proper cooling is essential for maintaining the integrity of the pellets during storage and transportation. If pellets are not adequately cooled, they may become soft and lose their shape, leading to quality issues. A well-designed cooling system can enhance the overall efficiency of the pellet production process. (Related post:Biomass Pellet Machine For Sale)
8. Maintenance and Wear Parts
Regular maintenance and the quality of wear parts significantly influence the performance of a small biomass pellet machine.
- Wear Parts: Components such as the die, rollers, and knives are subject to wear and should be replaced proactively based on operating hours and condition. Using high-quality replacement parts can improve machine performance and extend its lifespan.
- Maintenance Practices: Establishing a routine maintenance schedule that includes cleaning, lubrication, and inspection of components helps prevent breakdowns and ensures consistent pellet quality. Proper maintenance practices can significantly reduce downtime and production costs.
Conclusion
The performance of a small biomass pellet machine is greatly influenced by its key components, including the pellet die, rollers, feed hopper, conditioner, gearbox, motor, cooling system, and maintenance practices. Understanding how these components interact and affect the pelletizing process is essential for optimizing machine efficiency and output.
By selecting high-quality components and adhering to proper maintenance practices, producers can enhance the performance of their biomass pellet machines, resulting in improved pellet quality, increased production rates, and reduced operational costs. As the demand for renewable energy sources continues to rise, investing in a well-maintained and efficiently operating biomass pellet machine will be crucial for success in the biomass industry.