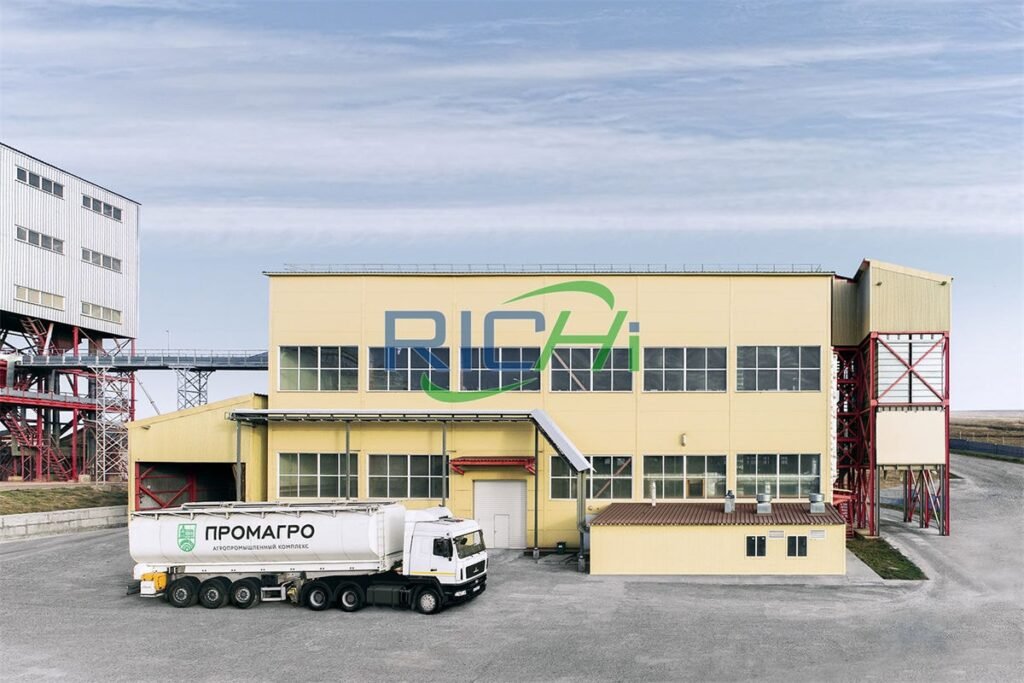
In the rapidly evolving landscape of aquaculture, the demand for high-quality and sustainable fish feed has become a critical factor driving the industry’s growth and success. As the world’s population continues to rise, and the need for protein-rich food sources intensifies, fish farming has emerged as a viable solution to meet this growing demand. However, ensuring the availability of nutritionally balanced and cost-effective fish feed is a paramount concern for aquaculture operations of all sizes. To address this need, fish feed mill plants have emerged as essential facilities, offering a comprehensive solution for efficient and sustainable fish feed production. However, establishing and operating these plants requires a significant investment, necessitating a thorough understanding of the associated costs and factors influencing them.
The Importance of Fish Feed Mill Plants
Fish feed mill plants play a pivotal role in supporting the growth and sustainability of the aquaculture industry. These specialized facilities offer numerous benefits:
- Consistent Product Quality: Advanced technologies and quality control measures ensure the production of fish feed with consistent nutrient profiles, promoting optimal fish health, growth, and productivity.
- Customized Formulations: The ability to manufacture feed formulations tailored to the specific nutritional needs of different fish species, life stages, and farming systems optimizes performance and efficiency.
- Efficient Production: Modern fish feed mill plants leverage automation and process optimization to maximize output and minimize waste, contributing to cost-effectiveness and sustainability.
- Sustainability: Incorporation of sustainable practices, such as the use of alternative protein sources, waste reduction strategies, and energy-efficient technologies, promotes environmental responsibility within the aquaculture industry.
- Economic Opportunities: Investing in fish feed mill plants creates employment opportunities, stimulates local economies, and contributes to the overall growth and development of the aquaculture sector.
Understanding Fish Feed Mill Plant Costs
Establishing and operating a fish feed mill plant involves a multitude of costs, which can be broadly categorized into capital expenditures (CAPEX) and operational expenditures (OPEX).
Capital Expenditures (CAPEX)
Capital expenditures represent the initial investment required to construct and equip the fish feed mill plant. These costs typically include:
- Land and Site Preparation: The acquisition of land and the necessary site preparation, including grading, drainage, and infrastructure development.
- Building and Infrastructure: The construction of the main production facility, storage areas, offices, and other supporting infrastructure.
- Machinery and Equipment: The purchase and installation of specialized machinery and equipment, such as grinders, mixers, pelleting systems, drying and cooling units, and automation systems.
- Auxiliary Systems: The implementation of auxiliary systems, including material handling equipment, dust collection systems, process control systems, and utilities.
- Permits and Regulatory Compliance: Costs associated with obtaining necessary permits, licenses, and ensuring compliance with relevant regulations and standards.
- Engineering and Project Management: Fees for professional services, such as engineering design, project management, and construction oversight.
Operational Expenditures (OPEX)
Operational expenditures encompass the ongoing costs associated with running and maintaining the fish feed mill plant. These fish feed mill plant costs may include:
- Raw Materials: The procurement of high-quality raw materials, such as fishmeal, plant-based proteins, vitamins, and minerals, is a significant recurring expense.
- Labor and Personnel: Salaries, wages, and benefits for skilled workers, including operators, maintenance staff, quality control personnel, and administrative staff.
- Energy and Utilities: Costs associated with electricity, water, and other utilities required for the plant’s operations.
- Maintenance and Repairs: Regular maintenance and repairs of machinery, equipment, and infrastructure to ensure optimal performance and longevity.
- Quality Control and Testing: Expenses related to laboratory testing, analysis, and quality control measures to ensure compliance with nutritional and safety standards.
- Transportation and Logistics: Costs associated with the transportation of raw materials and finished products, as well as logistics management.
- Regulatory Compliance and Certifications: Ongoing costs for maintaining compliance with relevant regulations, obtaining certifications, and adhering to industry standards.
- Overhead and Administrative Costs: Expenses related to general overhead, administrative functions, and management of the plant.
Factors Influencing Fish Feed Mill Plant Costs
The costs associated with establishing and operating a fish feed mill plant can vary significantly depending on several factors, including:
- Plant Size and Capacity: The scale of the plant, in terms of production capacity and throughput, directly impacts the capital investment required and the operational costs.
- Location and Infrastructure: The geographical location, availability of raw materials, transportation networks, and existing infrastructure can significantly influence both CAPEX and OPEX.
- Technology and Automation Level: The degree of automation and the incorporation of advanced technologies can increase initial capital costs but may lead to long-term operational efficiencies and cost savings.
- Regulatory Environment: The complexity and stringency of local regulations, environmental standards, and industry requirements can impact compliance costs and the overall investment required.
- Raw Material Availability and Pricing: Fluctuations in the availability and pricing of raw materials, such as fishmeal and plant-based proteins, can directly affect operational costs and profitability.
- Energy and Utility Costs: The cost of energy, water, and other utilities can vary significantly based on location and can have a substantial impact on operational expenses.
- Labor and Workforce Availability: The availability and cost of skilled labor in the local market can influence both capital and operational expenditures.
- Project Management and Execution: Effective project management and execution during the construction and commissioning phases can minimize delays, cost overruns, and potential operational inefficiencies.
Cost Optimization and Sustainability Strategies
To maximize the return on investment and ensure long-term profitability, fish feed mill plant operators must adopt cost optimization and sustainability strategies. These may include:
- Continuous Process Improvement: Implementing lean manufacturing principles, process optimization, and continuous improvement initiatives to enhance efficiency and reduce waste.
- Energy Efficiency Measures: Investing in energy-efficient technologies, such as heat recovery systems, and exploring renewable energy sources to reduce energy costs and environmental impact.
- Waste Reduction and Recycling: Implementing waste reduction strategies, such as utilizing by-products and exploring recycling opportunities, can minimize waste disposal costs and promote sustainability.
- Supply Chain Optimization: Optimizing the supply chain through strategic sourcing, inventory management, and logistics planning can reduce raw material costs and transportation expenses.
- Workforce Training and Development: Investing in workforce training and development programs can enhance productivity, reduce operational errors, and promote a culture of continuous improvement.
- Collaboration and Partnerships: Exploring collaborative opportunities with industry partners, research institutions, and government agencies can facilitate knowledge sharing, access to innovative technologies, and potential cost-sharing initiatives.
- Alternative Protein Sources: Exploring the use of alternative protein sources, such as insect meal, algae, or plant-based proteins, can reduce reliance on traditional fishmeal and contribute to cost savings and sustainability.
- Precision Aquaculture Nutrition: Adopting precision aquaculture nutrition techniques, including individualized feeding strategies and real-time monitoring, can optimize feed utilization and minimize waste, leading to cost savings and improved environmental performance.
In conclusion, establishing and operating a fish feed production line requires a significant investment, with costs spanning capital expenditures and ongoing operational expenses. By understanding the various cost components and the factors influencing them, aquaculture industry stakeholders can make informed decisions and develop strategies to optimize their investments. Additionally, embracing sustainability practices and continuous improvement initiatives can not only reduce costs but also contribute to the long-term viability and competitiveness of the fish feed mill plant, supporting the growth and sustainability of the aquaculture industry as a whole.
For details please contact: Richi Machinery
WhatsApp:86 138 3838 9622
Email:enquiry@richipelletmachine.com