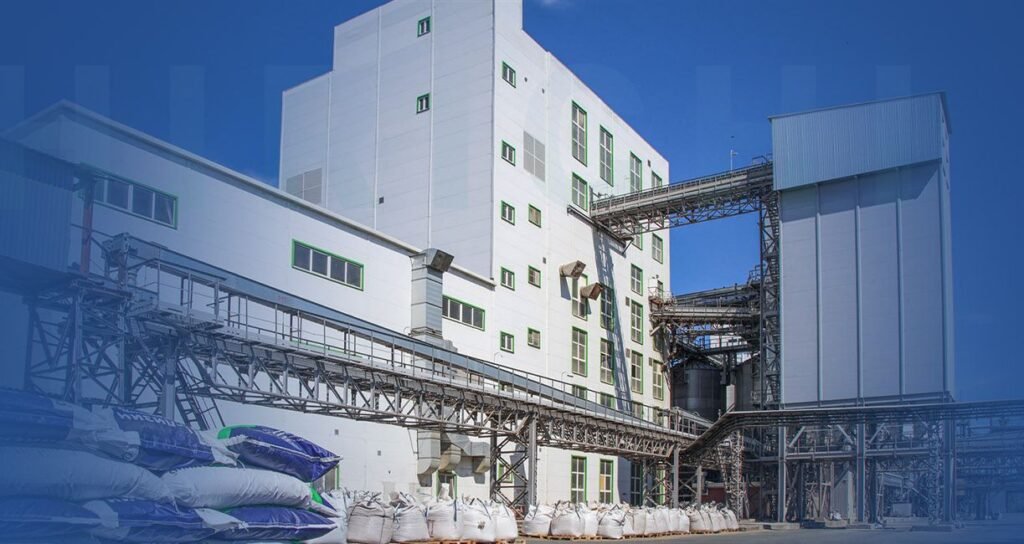
Feed mill engineering projects, particularly those with a capacity of 15 tons per hour (t/h), require regular maintenance to ensure optimal performance, longevity of equipment, and adherence to safety and quality standards. Understanding the daily maintenance costs associated with such a facility is crucial for effective budgeting and operational planning. This article explores the various components of daily maintenance costs for a 15t/h feed mill and provides insights into managing these expenses efficiently.
Components of Daily Maintenance Costs
- Routine Equipment Inspections and Servicing
Daily equipment checks are essential to prevent unexpected breakdowns and ensure smooth operations. This includes:
- Lubrication of moving parts
- Checking and adjusting belt tensions
- Inspecting wear parts such as dies and rollers in pellet mills
- Cleaning of critical components
Estimated daily cost: $150 – $250
- Replacement of Wear Parts
Certain components in a feed mill experience regular wear and tear and require frequent replacement:
- Hammer mill screens and hammers
- Pellet mill dies and rollers
- Conveyor belts and bucket elevator cups
While these are not daily expenses, when averaged over time, they contribute to the daily maintenance cost.Estimated daily cost (averaged): $100 – $200
- Cleaning and Sanitation
Maintaining a clean and hygienic environment is crucial in feed production:
- Daily cleaning of mixing equipment
- Sanitizing storage bins and conveyors
- Dust control measures
Estimated daily cost: $100 – $150
- Preventive Maintenance Labor
Skilled technicians are required to perform daily maintenance tasks:
- 1-2 full-time maintenance technicians
- Occasional specialized technician visits
Estimated daily cost: $200 – $300
- Spare Parts Inventory
Maintaining an inventory of commonly needed spare parts is essential for quick repairs:
- Bearings, belts, and seals
- Electrical components
- Specialized parts for critical equipment
While not a direct daily expense, the cost of maintaining this inventory can be averaged.Estimated daily cost (averaged): $50 – $100
- Energy Costs for Maintenance Activities
Some maintenance activities require additional energy consumption:
- Running equipment for testing after maintenance
- Powering cleaning equipment
- Lighting and HVAC for maintenance areas
Estimated daily cost: $30 – $50
- Consumables and Supplies
Various consumables are used in daily maintenance:
- Lubricants and greases
- Cleaning agents and sanitizers
- Small tools and personal protective equipment (PPE)
Estimated daily cost: $50 – $100
- Environmental Compliance and Waste Management
Proper disposal of waste generated during maintenance and adherence to environmental regulations incur costs:
- Disposal of used oils and chemicals
- Maintenance of dust collection systems
- Compliance with local environmental regulations
Estimated daily cost: $30 – $60
- Maintenance Management Software and Systems
Modern feed mills often use computerized maintenance management systems (CMMS) to track and schedule maintenance activities:
- Software licensing fees
- Training and updates
- Hardware maintenance
Estimated daily cost (averaged): $20 – $40
- Unexpected Repairs and Emergency Maintenance
While not strictly “daily” costs, provisions must be made for unexpected breakdowns:
- Emergency repair labor
- Expedited parts shipping
- Production downtime costs
Related post:https://www.richipelletmachine.com/compound-feed-mill/
Estimated daily cost (averaged over time): $100 – $200
Total Estimated Daily Maintenance Cost
Based on these components, the total estimated daily maintenance cost for a 15t/h feed mill engineering project ranges from $830 to $1,450 per day.Factors Influencing Maintenance CostsSeveral factors can influence the daily maintenance costs:
- Age of Equipment: Older equipment generally requires more frequent maintenance and replacement of parts.
- Operational Hours: Mills operating 24/7 will incur higher maintenance costs compared to those with shorter operational hours.
- Feed Types Produced: Different types of feed can cause varying degrees of wear on equipment.
- Environmental Conditions: Harsh environments (e.g., high humidity, extreme temperatures) can accelerate equipment wear.
- Quality of Initial Equipment: Higher quality equipment may have higher upfront costs but often results in lower maintenance costs over time.
- Maintenance Strategy: Proactive maintenance strategies can reduce overall costs compared to reactive approaches.
- Staff Expertise: Well-trained staff can perform maintenance more efficiently and effectively.
Strategies for Optimizing Maintenance Costs
To manage and potentially reduce daily maintenance costs, consider the following strategies:
- Implement Predictive Maintenance: Use sensors and data analytics to predict when maintenance is needed, reducing unnecessary interventions.
- Invest in Staff Training: Well-trained staff can perform maintenance more efficiently and identify potential issues early.
- Standardize Equipment: Using standardized equipment across the facility can reduce the variety of spare parts needed and simplify maintenance procedures.
- Optimize Inventory Management: Implement just-in-time inventory practices for spare parts to reduce carrying costs while ensuring availability.
- Energy Efficiency Measures: Invest in energy-efficient equipment and practices to reduce overall operational costs, including those related to maintenance.
- Regular Equipment Upgrades: Periodically upgrading to more efficient and reliable equipment can reduce long-term maintenance costs.
- Develop Strong Supplier Relationships: Good relationships with equipment suppliers can lead to better support, faster parts delivery, and potentially lower costs.
Conclusion
The daily maintenance cost of a 15t/h feed mill engineering project is a significant but necessary expense, ranging from $830 to $1,450 per day. This investment in maintenance is crucial for ensuring the longevity of equipment, maintaining product quality, and preventing costly breakdowns and production interruptions.
While these costs may seem substantial, they should be viewed in the context of the overall operational budget and the potential costs of equipment failure or production downtime. Proper maintenance not only prevents these larger expenses but also contributes to the efficiency and productivity of the feed mill.
By implementing strategic maintenance practices, investing in staff training, and adopting modern maintenance management systems, feed mill operators can optimize their maintenance costs while ensuring high-quality feed production. Regular review and adjustment of maintenance practices can help balance the need for thorough equipment care with cost-effectiveness, ultimately contributing to the long-term success and profitability of the feed mill operation.
For details please contact: pelletizer
WhatsApp:86 138 3838 9622
Email:enquiry@richipelletmachine.com