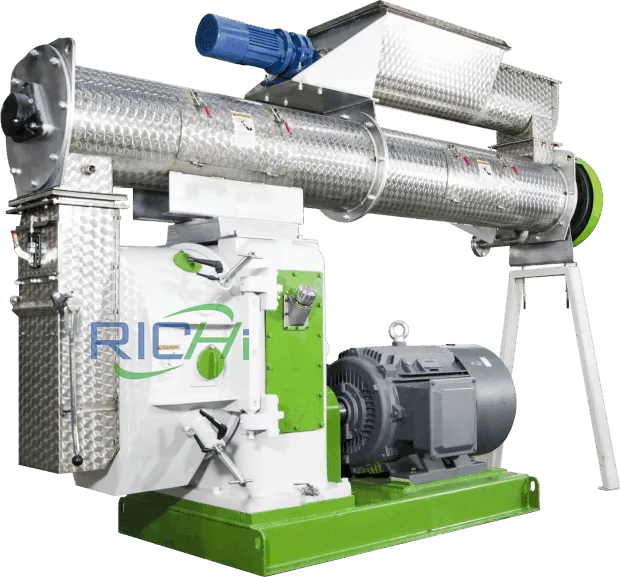
Introduction
Poultry farming is one of the fastest-growing sectors in global agriculture, driven by rising demand for meat and eggs. As operations scale up, feed efficiency becomes a critical determinant of profitability. For medium and large poultry farms, the adoption of a poultry feed pellet machine can significantly improve feed utilization and reduce operating costs.
This article presents a comprehensive cost-benefit analysis of poultry feed pellet machines, examining their financial and operational impact. From capital investment to long-term savings, we explore how these machines empower commercial-scale poultry farms to boost productivity, ensure consistent quality, and secure competitive advantages.
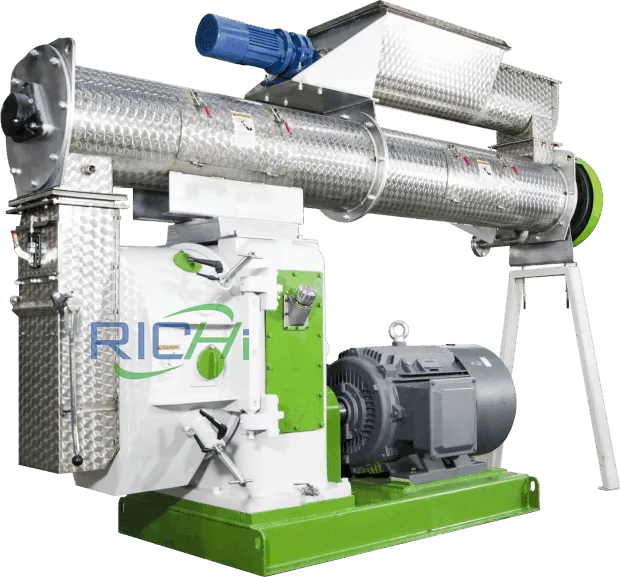
1. What Is a Poultry Feed Pellet Machine?
A poultry feed pellet machine is a mechanical device that compresses raw feed materials into dense, uniform pellets suitable for poultry consumption. These machines are available in different capacities, from 300 kg/h for small farms to 10 tons/h or more for large-scale operations.
They typically consist of:
- Feeder system – to control raw material input
- Conditioner – to introduce steam and soften materials
- Pelletizing chamber – with a die and rollers
- Cutter and discharge – to shape and release pellets
- Cooling and screening units – in larger configurations
For commercial poultry farms, these systems are often part of an integrated feed production line.
2. Initial Investment Breakdown
The upfront cost of a poultry feed pellet machine varies depending on the following factors:
Machine Capacity | Power (kW) | Price Range (USD) |
---|---|---|
1–2 t/h | 37–45 | $15,000–$30,000 |
3–5 t/h | 55–90 | $35,000–$60,000 |
6–10 t/h | 110–160 | $70,000–$120,000 |
10+ t/h (plant) | 200+ | $150,000–$300,000+ |
Additional costs may include:
- Raw material processing (grinders, mixers)
- Steam boilers (for conditioner units)
- Cooling and drying systems
- Installation and commissioning
- Operator training
- Electrical infrastructure upgrades
While these figures may seem steep, the return on investment (ROI) is often rapid, especially when considering operational savings.
3. Operational Costs: Key Considerations
To calculate the total cost of ownership, consider the following recurring costs:
A. Energy Consumption
Pellet machines consume electricity or diesel. On average:
- 1 ton of pellets = ~50–70 kWh of electricity
- Cost per kWh varies: $0.05 to $0.20, depending on country and region
B. Labor
Automated systems reduce labor needs, but manual tasks like raw material prep and machine monitoring still require staff.
- Labor: 2–5 workers for 5–10 t/h line
- Monthly wages: $300–$800 per worker depending on region
C. Maintenance
Routine maintenance includes:
- Die and roller replacement (every 600–1,000 hours)
- Lubrication and bearing checks
- Electrical panel servicing
- Belt and gear checks
Annual maintenance cost: 3%–5% of machine value
D. Raw Materials
Input ingredients include maize, soy, wheat bran, oil cake, bone meal, vitamins, and more. In-house sourcing or contract farming can further reduce feed costs.
4. Feed Cost Savings: The Game Changer
Feed typically represents 60%–70% of poultry production costs. Buying commercial feed exposes farms to:
- Price volatility
- Transport costs
- Quality inconsistencies
- Limited formulation control
With a poultry feed pellet machine, farms can:
- Use local raw materials
- Formulate custom rations for growth stages
- Improve feed conversion ratio (FCR)
- Reduce feed waste through pelletization
Case Study Calculation:
Metric | Without Pellet Machine | With Pellet Machine |
---|---|---|
Feed cost/ton | $450 | $320 |
Daily feed consumption (5,000 birds) | 1.5 tons | 1.5 tons |
Daily feed cost | $675 | $480 |
Monthly feed cost | $20,250 | $14,400 |
Monthly savings | — | $5,850 |
Annual savings | — | $70,200 |
This estimate shows how a mid-sized farm can recover equipment investment in under 2 years through feed cost reduction alone.
5. Performance Benefits: Maximizing Output
Using pelleted feed improves poultry performance:
- Better FCR: From 2.1 down to 1.7 in some broilers
- Faster growth: Birds reach market weight sooner
- Higher egg yield: Due to balanced nutrition
- Lower mortality: From improved digestibility and gut health
These performance improvements translate to more meat or eggs per unit of feed, multiplying the benefits beyond raw cost savings.
6. Value Addition and Business Expansion
A poultry feed pellet machine is not just a tool for internal use—it can become a new revenue stream. Farms can:
- Sell surplus feed to nearby smallholders
- Create brand identity for organic or specialty feed
- Offer contract pelletizing for others with raw materials
- Diversify into multi-species feed (fish, pigs, cattle)
Adding packaging, labeling, and traceability features can further enhance value-added offerings.
7. Tax and Subsidy Benefits
Governments in many countries support agricultural mechanization and feed self-sufficiency. Financial benefits may include:
- Import duty waivers on machinery
- Tax deductions on capital equipment
- Subsidies or grants for renewable energy integration
- Access to low-interest agribusiness loans
- Carbon credit eligibility for energy-efficient systems
These incentives significantly reduce the effective cost of acquiring a poultry feed pellet machine.
8. Risk Mitigation Through Self-Sufficiency
Medium and large poultry farms face supply chain risks such as:
- Delayed feed deliveries
- Shortages during harvest or crisis periods
- Quality scandals or contamination
- Currency exchange fluctuations (for imported feed)
By producing feed on-site, farms:
- Gain greater control over supply and quality
- Stabilize operating costs in volatile markets
- Improve traceability and compliance with food safety standards
Self-reliant feed production is a major competitive advantage in uncertain economic or geopolitical climates.
9. Case Study: 8 t/h Feed Pellet Line in South Africa
A commercial poultry farm with 100,000 broilers per cycle installed a fully automated 8 t/h poultry feed pellet line.
Key outcomes:
- Capital investment: $160,000
- Payback period: 18 months
- Feed cost reduction: 28%
- FCR improvement: from 2.0 to 1.68
- Revenue from surplus feed: $20,000 annually
- Reduction in mortality: 3.5% → 1.2%
The farm now supplies feed to smaller producers in the region and is exploring exports to neighboring countries.
10. Expert Tips for Maximizing ROI
To achieve the best return on your poultry feed pellet machine investment:
- Buy from reputable suppliers with after-sales service
- Choose modular designs for future expansion
- Use local ingredients to reduce transport costs
- Employ experienced nutritionists for optimal formulations
- Implement regular maintenance schedules
- Train operators for safe, efficient machine use
- Track performance metrics like FCR, mortality, feed costs, etc.
Data-driven management ensures that the feed mill becomes a profit center, not just a utility.
Conclusion
For medium and large poultry farms, a poultry feed pellet machine is not a luxury—it’s a strategic investment that can dramatically reduce costs, improve animal performance, and secure long-term sustainability. By enabling on-site feed production, these machines help poultry producers lower feed costs, ensure quality control, and unlock new business opportunities.
With payback periods as short as 12–24 months and additional benefits in risk mitigation, brand development, and product diversification, the value of pelletization technology is clear. As feed prices continue to rise and markets become more competitive, those who invest in feed autonomy today will lead the poultry industry of tomorrow.