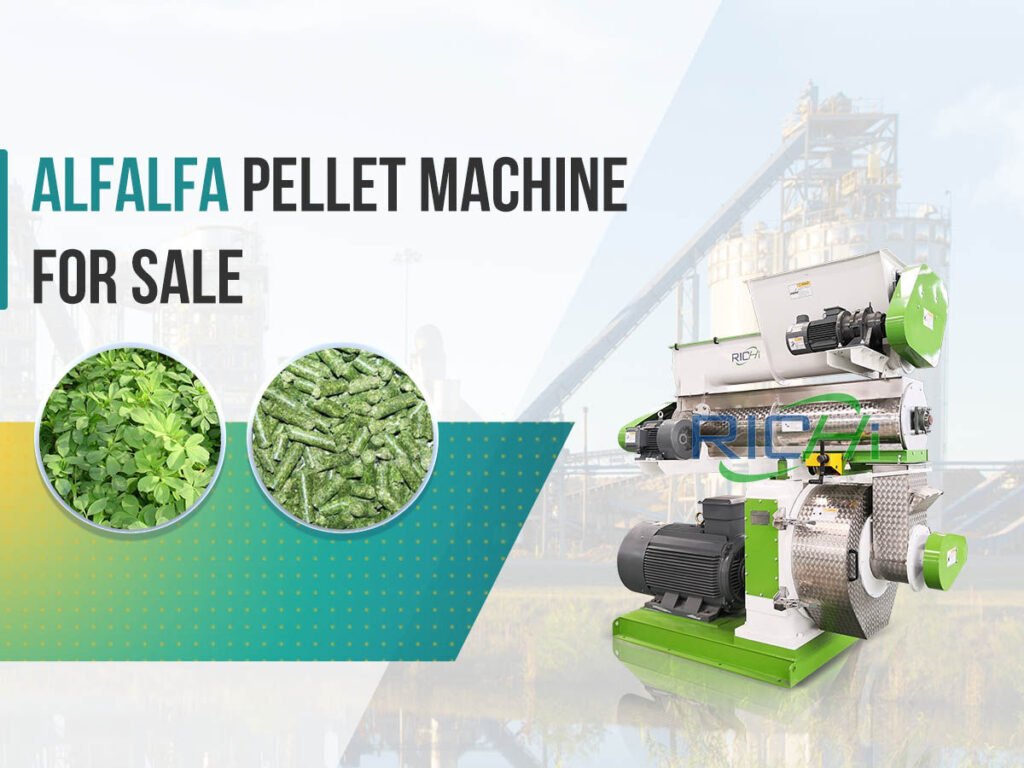
Alfalfa pellet making machine is a specialized piece of equipment designed to compress raw alfalfa material into compact pellets. These pellets serve as a convenient and efficient feed source for livestock, poultry, and other animals. Let’s delve into the intricacies of alfalfa pellet making machines, analyzing their applications, classification, working principles, and practical value in the industry.
Applications in the Industry:
The demand for alfalfa pellets in the agricultural industry has been steadily increasing, driven by factors such as the growing awareness of the importance of high-quality feed and the rise of intensive livestock farming practices.
According to recent industry reports, the global market for alfalfa pellets reached $3.5 billion in 2020, with an expected compound annual growth rate (CAGR) of 4.5% from 2021 to 2026. This data underscores the significant market opportunity for alfalfa pellet making machines, particularly in regions with a strong presence of livestock and poultry farming.
Classification and Working Principle:
Alfalfa pellet machines are classified into two main categories: flat die pellet mills and ring die pellet mills. Flat die pellet mills are suitable for small to medium-scale production, with capacities ranging from 50 kg/h to 500 kg/h. In contrast, ring die pellet mills are more suitable for large-scale production, with capacities ranging from 1 ton/h to 100 tons/h or more.
The working principle of both types of machines involves compressing raw alfalfa material through a die under high pressure. This process results in the formation of compact pellets with consistent size and density, ensuring uniform feed quality.
How to Choose The Alfalfa Pellet Making Machine:
When selecting an alfalfa pellet machine, several factors should be considered. These include production capacity, pellet quality, energy efficiency, and after-sales support.
For small-scale operations, a flat die pellet mill may be sufficient, while larger operations may require the higher throughput and efficiency offered by a ring die pellet mill. It is essential to choose a reputable supplier that offers customized solutions tailored to the specific needs of the customer’s pellet production line.
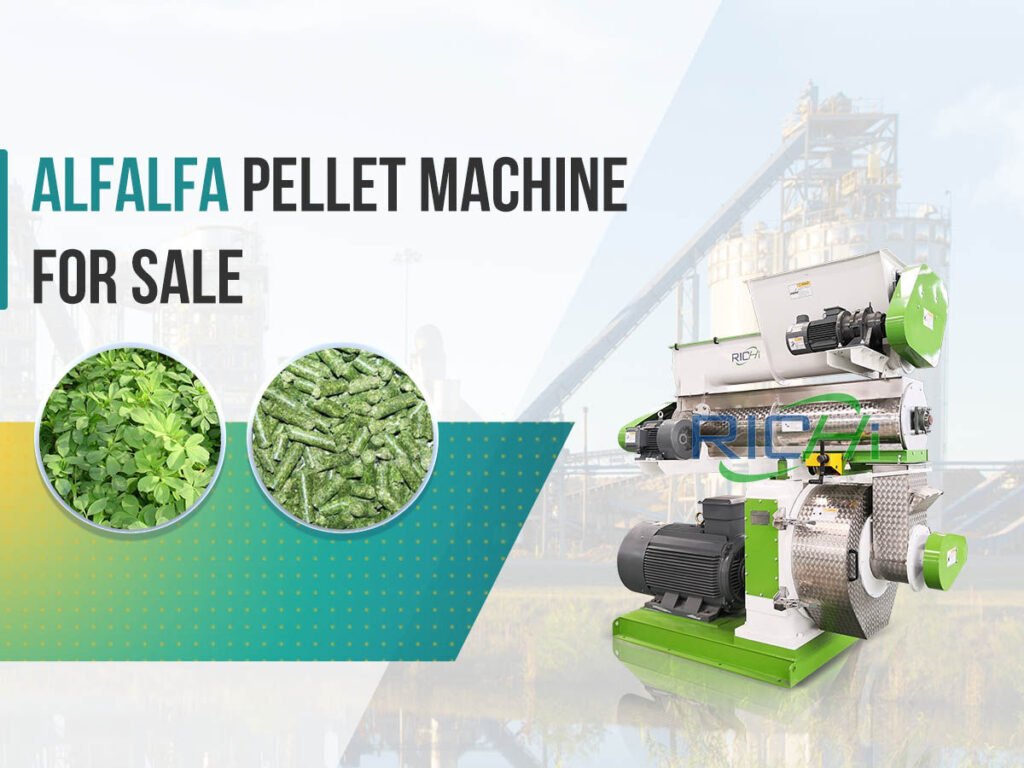
Choosing a Pellet Machine Supplier:
RICHI Machinery Company is a trusted manufacturer of alfalfa pellet making machines, with a proven track record of delivering high-quality equipment and exceptional customer service. With over 20 years of experience in the industry, RICHI Machinery has successfully installed pellet production lines in over 100 countries worldwide.
Their team of engineers and technicians specializes in site design and turnkey projects, ensuring seamless integration of equipment and optimal performance. RICHI Machinery’s commitment to innovation and customer satisfaction makes them a preferred choice for feed producers and farmers seeking reliable and efficient pellet making machines.
Practical Application Value:
The practical application value of alfalfa pellet making machines lies in their ability to enhance feed quality, reduce costs, and optimize animal nutrition. By investing in high-quality equipment and partnering with experienced suppliers like RICHI Machinery, feed producers and farmers can achieve higher production efficiency, increased profitability, and long-term success in their operations.
With the global demand for high-quality feed on the rise, alfalfa pellet making machines offer a sustainable solution for meeting the evolving needs of the agricultural industry.
Navigating Alfalfa Pellet Production Lines: Case Studies and Solutions
Alfalfa pellet production lines are critical for meeting the demands of the ever-growing agricultural industry. This article explores several project cases ranging from 5 to 100 tons per hour, analyzing encountered challenges and their solutions, with a focus on RICHI Machinery’s turnkey project capacity.
Case Study 1: 10 Tons/Hour Alfalfa Pellet Production Line
Program Design Problems: Designing an efficient program for the 10 tons/hour production line posed challenges in balancing production capacity, energy consumption, and pellet quality. RICHI Machinery’s engineering team conducted extensive simulations and optimization studies to develop a customized program that maximized efficiency while ensuring consistent pellet quality.
Site Problems: Limited space at the client’s site necessitated careful planning and layout optimization to accommodate the production line. RICHI Machinery’s site design experts conducted a thorough assessment and proposed a compact layout that optimized space utilization without compromising workflow efficiency.
Equipment Problems: During equipment installation, technical issues were encountered with the pelletizing machine’s drive system, resulting in production delays. RICHI Machinery’s on-site technicians quickly identified the problem and implemented necessary adjustments to restore the machine’s functionality, minimizing downtime and ensuring uninterrupted production.
Installation Problems: Coordinating the installation of various equipment components and systems posed logistical challenges. RICHI Machinery’s project management team efficiently coordinated the installation process, ensuring timely completion and proper integration of all components.
After-sales Problems: After commissioning the production line, the client faced challenges in operating and maintaining the equipment effectively. RICHI Machinery provided comprehensive training sessions for the client’s staff, empowering them with the necessary skills and knowledge to maximize equipment performance and minimize downtime.
Case Study 2: 50 Tons/Hour Alfalfa Pellet Production Line
Program Design Problems: Optimizing the production process to achieve the desired output while minimizing energy consumption and production costs presented challenges. RICHI Machinery’s engineers conducted rigorous testing and optimization to develop a customized program tailored to the client’s specific requirements.
Site Problems: Harsh environmental conditions at the client’s site, including temperature fluctuations and dust exposure, posed challenges to equipment performance. RICHI Machinery’s engineers implemented innovative solutions such as climate control systems and dust suppression measures to mitigate the impact of environmental factors on production efficiency.
Equipment Problems: Technical issues with the cooling system resulted in inconsistent pellet quality and production bottlenecks. RICHI Machinery’s technical support team conducted a thorough assessment and implemented necessary upgrades to optimize cooling efficiency and ensure uniform pellet quality.
Installation Problems: Coordinating the installation of complex equipment components and systems required meticulous planning and coordination. RICHI Machinery’s experienced installation team executed the installation process with precision, ensuring proper alignment and functioning of all equipment components.
After-sales Problems: Following installation, the client faced challenges in equipment operation and maintenance. RICHI Machinery provided ongoing support and maintenance services, including remote monitoring and troubleshooting, to ensure optimal equipment performance and minimize downtime.
In conclusion, navigating the complexities of alfalfa pellet production lines requires expertise, experience, and innovative solutions. With RICHI Machinery’s turnkey project capacity and commitment to customer satisfaction, clients can overcome challenges and achieve success in their feed production endeavors.